University team undertakes research led by Zeeko Ltd to unlock abundant energy
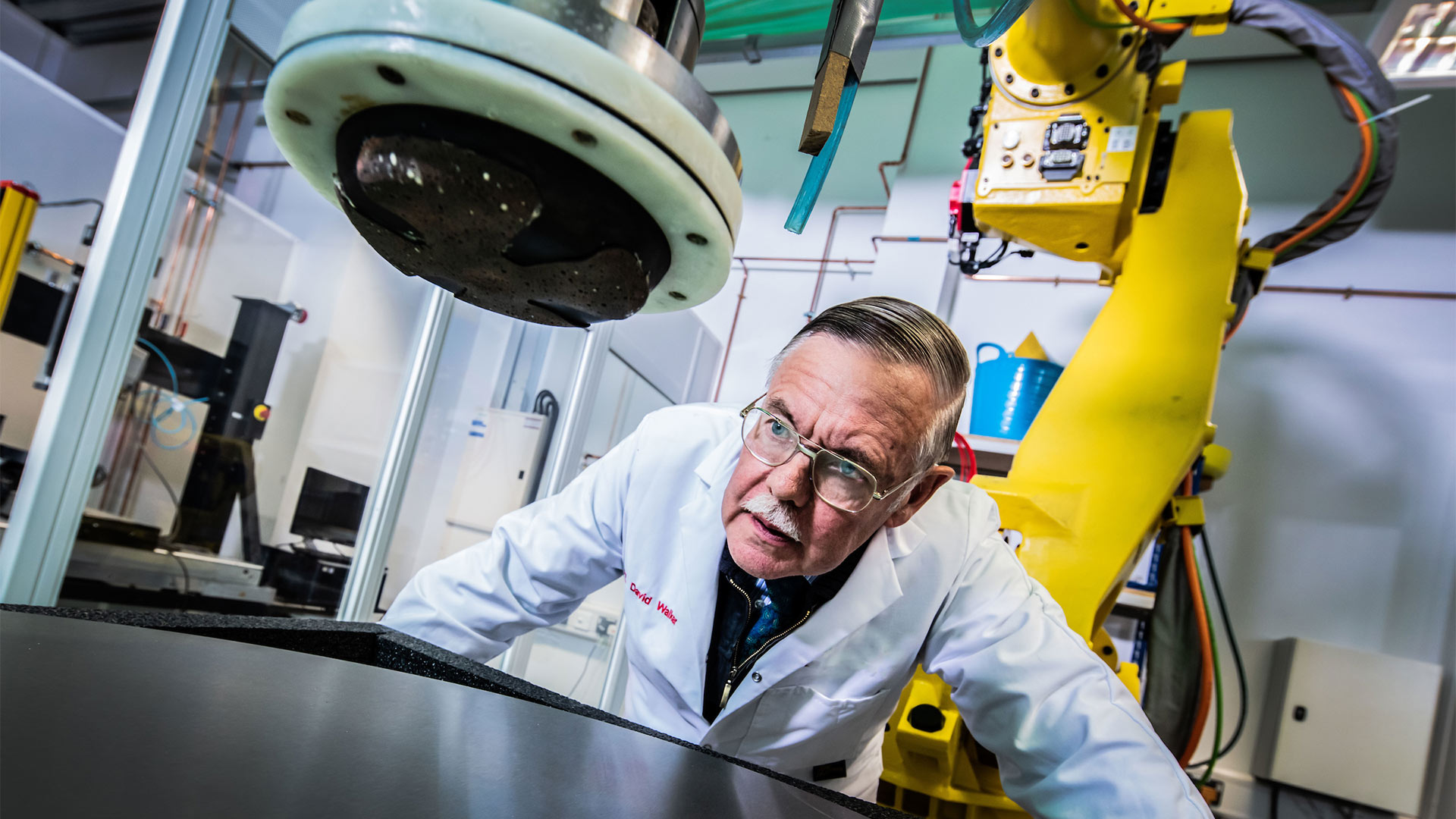
(Image: Professor David Walker of The University of Huddersfield’s Laboratory for Ultra Precision Surfaces)
A University of Huddersfield research team is working on an international breakthrough project that could provide a key to unlocking a safe green energy solution without hazardous waste.
Titled Super-polished Freeforms Optics Systems (SFOS) for industry and nuclear fusion, the research and development project is led by UK firm Zeeko, which specialises in the manufacture of ultra-precision polishing machines.
The total funding for the consortium amounts to €3.6 million and will seek to advance the manufacture of nano-scale-accurate super-smooth optics with complex ‘freeform’ surfaces for safe energy generation by laser-fusion.
The team at the University’s Laboratory for Ultra Precision Surfaces is lending its expertise to the three-year project, which also involves another UK firm, Thin Metal Films Limited, as well as a Swiss company and University.
Innovate UK funds the UK portion of the research – at £1.5 million in total, with £559,000 of that figure being granted to the University. Meanwhile, Innosuisse, the Swiss Innovation Agency, is funding the research in Switzerland at the Applied University OST and WZW Optic AG.
The Huddersfield laboratory is part of the University’s Centre for Precision Technologies and is located off-campus at Sci-Tech Daresbury, the National Science and Enterprise Campus in Cheshire.
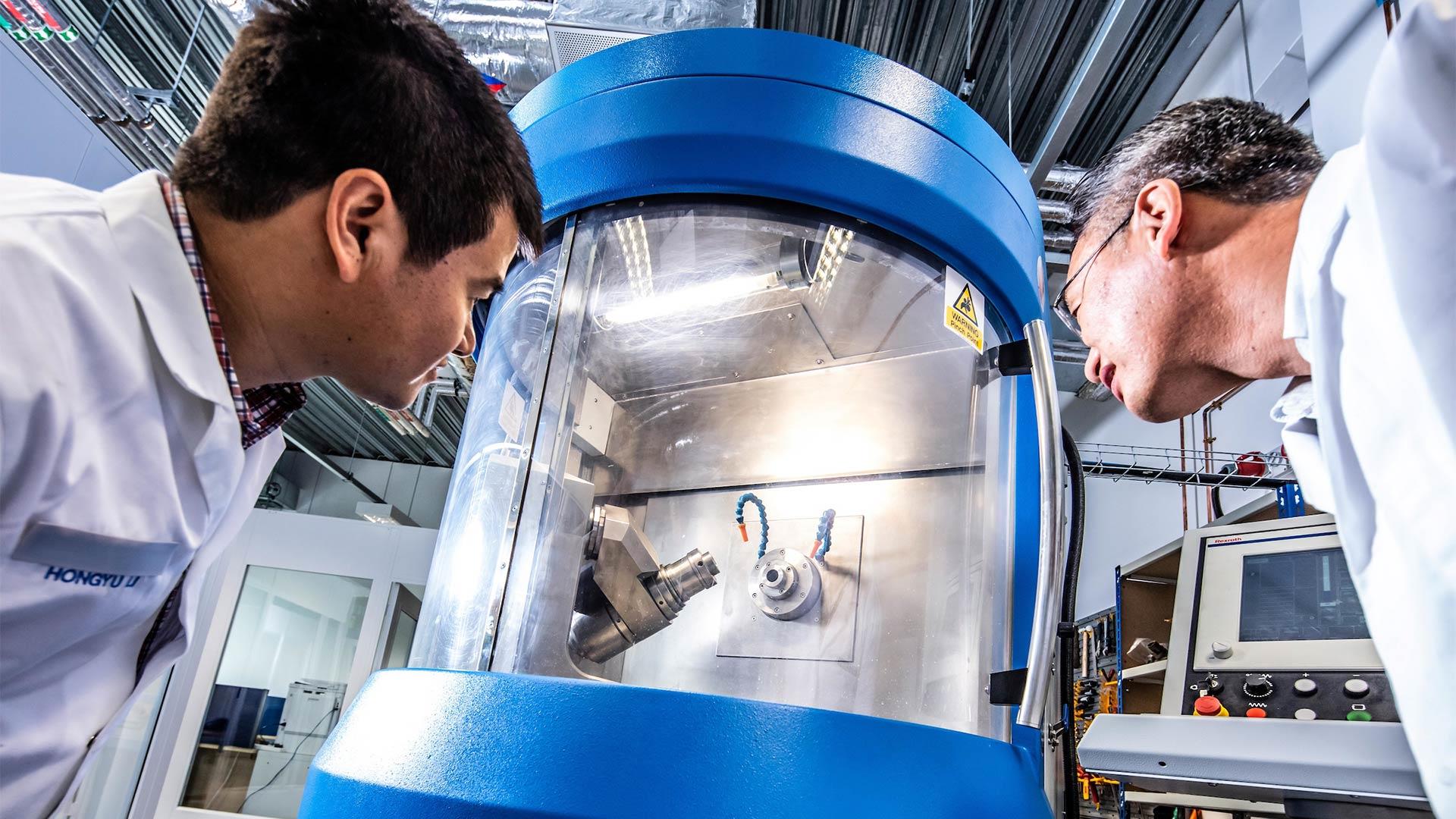
Professor David Walker heads up the University’s Daresbury facility. But on this project, he is providing the scientific leadership under his role as Research Director of Zeeko Ltd.
Professor Walker explained that, in the last year, scientists at the US National Ignition Facility surpassed their target of energy break-even – producing more energy out of their hydrogen fuel pellet, than the laser energy input.
He said: “This was a huge milestone and it shows the feasibility of the whole concept. But the problem is that, while they have indeed exceeded break-even at the fuel pellet, if you look at the total energy budget – the electricity needed to power the lasers involved, compared to the total energy back – the overall efficiency is only a couple of per cent. Why? Because of the huge system complexity and losses in creating 192 high-power laser beams and focussing them all on one 2mm pellet.
“So how can you make systems like this more efficient? That is where freeform surfaces come in – there are more mathematical ‘knobs to twiddle’ in the design, enabling superior performance to be delivered with fewer optical surfaces. Achieving this is where our project comes in.
“For high power laser applications, you need surface qualities which are achievable on simple surfaces, but well beyond the state-of-the-art on freeforms. What we want to do is to push the boundaries of what is possible, to enable freeform surfaces with this exquisite quality.”
Professor Walker added that he presented the project at the UK Inertial Confinement Fusion Consortium Meeting in London in March, where it attracted considerable interest.
Discover more about Engineering and Technology courses at Huddersfield
The University's Centre for Precision Technologies is a centre of excellence for collaborative metrology research, solving real-world manufacturing problems through cutting-edge research in precision engineering.
Dr Guoyu Yu is leading the University of Huddersfield’s involvement in the ground-breaking project.
He said: “We believe that, to make super smooth freeform optics, the ability to measure them is vital. So we are developing a hybrid metrology system so that our polishing technology can achieve the targets needed.
“Our Swiss partners have already developed some super smooth surfaces technology on simple surfaces that they will transfer to us, so that we can extend this to freeform surfaces.
“We are confident that our international consortium has the expertise to achieve the milestones and outcomes needed here.”
It is intended that the technology will also have a wider application in other areas such as medical instruments and scientific instrumentation.