“The proposed sensor solution has the potential to not only transform how Network Rail manages its rail lubrication programme but also rail infrastructure managers around the world,” says Network Rail's project lead James Lineton
THE University of Huddersfield has forged a partnership with an innovative technology business to work with Network Rail on developing a safer and more reliable track lubrication measurement system.
The collaboration will allow the University’s award-winning Institute of Railway Research (IRR) to work with Sheffield-based small and medium enterprise (SME) Tribosonics Ltd to develop a novel solution to the problem of detecting whether a critical form of lubrication is present between a railway wheel and the track.
In partnership with Network Rail and funded through its commitment to the EU Horizon 2020 Shift2Rail research programme, the advanced sensor solution will utilise ultrasonic technology, which is relatively new to the railway industry, as the basis of the detection method.
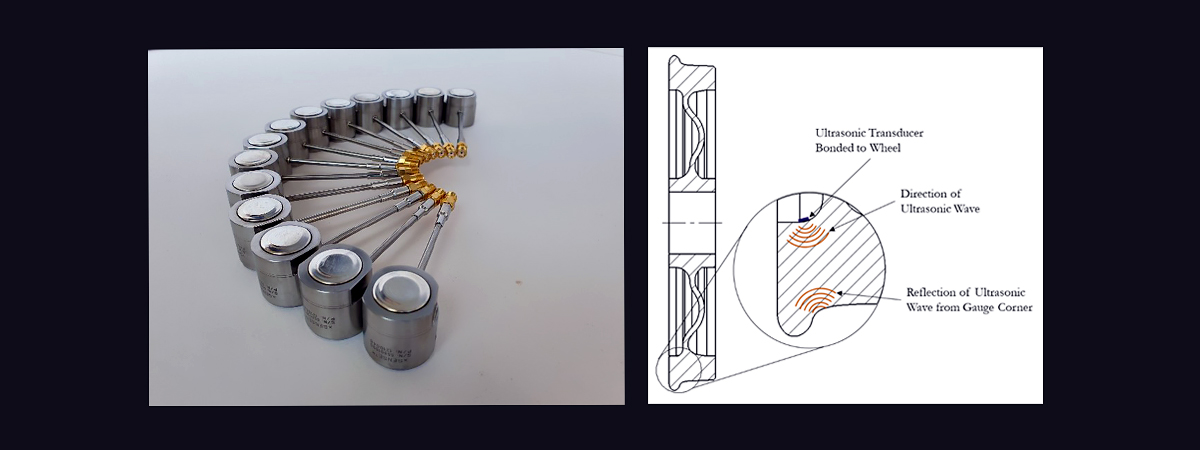
Professor Paul Allen, the University’s IRR Assistant Director who developed the concept, outlined the need for such technology.
“This measurement technology will provide an automated vehicle-mounted system that will communicate to Network Rail the presence of lubrication, and critically, locations where it is absent, thereby reducing maintenance costs and improving railway safety,” Professor Allen explained.
“It is not commonly known outside railway circles,” he continued, “that in curved track, a special type of grease is applied between the wheel and rail. This lubrication is applied to reduce wear but also the risk of derailment, whereby in some circumstances the wheel can climb up and over the railhead.
“Network Rail currently uses manual inspection techniques to determine whether lubrication is present. This approach requires maintenance staff to conduct on-track working and is a scenario Network Rail is looking to reduce,” he said.
According to Matthew Harmon from Tribosonics, the use of ultrasonic technology for detection of lubrication films is new to the railway industry but is widely used in other industries and a perfect fit for this application.
“Embedding ultrasonic sensors into the wheel provides the opportunity for continuous monitoring of lubrication effectiveness and allows preventative measures to be applied before problems arise,” he said.
“Processing the data outputs to ensure the key, relevant metric is obtained and presented in an accessible way forms a large part of this development.”
The detection system and related hardware will be developed by Tribosonics Ltd, with testing and sensor development carried out using the IRR’s HAROLD full-scale bogie test facility. Experimental trials will be conducted under real-world conditions, with axle loads of up to 25 tons and a target operating of 200kph.
Network Rail project lead James Lineton says the proposed sensor solution has the potential to not only transform how Network Rail manages its rail lubrication programme but also rail infrastructure managers around the world.
“By reducing downtime for maintenance activities, we can increase capacity, ultimately improving train availability for passengers,” he said.
Latest news from the Institute of Railway Research
Latest news from the Institute of Railway Research - 0 articles matching your search
Latest news from the Institute of Railway Research - 1 article matching your search
Latest news from the Institute of Railway Research - {{numberOfPosts}} articles matching your search