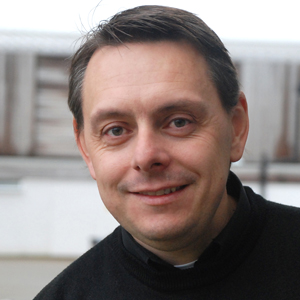
Alan Smith
Professor of Biopolymer Science
The methodology developed, named 'suspended layer additive manufacture', uses hydrogel with self-healing properties for structure stability
SCIENTISTS at the University of Huddersfield have spearheaded the development of a new technique for using 3D printing to produce soft gel medical implants customised to the needs of individual patients.
Replacement heart valves and blood vessels, plus artificial skin, bespoke drug delivery systems and smart dressings tailored to treat deep tissue wounds are among the many potential uses of a technique that has been named SLAM – suspended layer additive manufacture. Now, a major UK consortium that supports medical innovation is to explore its full potential, including the production of full thickness skin models.
“We will present our work to different medical professions. Almost every time I speak about it, people suggest new uses,” said one of the researchers behind the development of SLAM, Alan Smith, who is the University of Huddersfield’s Professor of Biopolymer Science.
The latest phase of the research is described in a new article that appears in the journal Advanced Functional Materials. It is co-written by Professor Smith, alongside collaborators at the University of Birmingham, and the lead author is Jessica Senior, who is completing her PhD research at the University Huddersfield, where she has carried out most of the 3D printing of the structures illustrated in the article. She talks about the project and demonstrates the technique in an online video recorded at an earlier phase of the research.
Researcher Jessica Senior explains the medical research aided by the Inkredible Bioprinter
3D printing of human tissue
The problem addressed by the team is that during the 3D printing process, soft materials with low viscosity quickly sag, so that the structure collapses. Various remedies have been developed, but the new Advanced Functional Materials article demonstrates that SLAM provides a solution by using a hydrogel with self-healing properties so that the structure does not sag. It enables the creation of intricate, layered structures and therefore a wide range of replacement body parts and other medical products.
The project, which could culminate in doctor’s surgeries being routinely equipped with 3D printers, is continuing.
“We are currently working on a project to produce full thickness skin models,” said Professor Smith. This would enable the treatment of very deep chronic wounds by simulating the different layers of skin tissue.
This project is now supported by Grow MedTech, a major UK programme providing specialist support for innovation in medical technologies, involving a consortium of six universities across the Leeds and Sheffield City Regions. Through Grow MedTech’s early stage innovation support, the project has gained access to both funding and a team of skilled and experienced advisors to help the team progress the development of SLAM.
More Stories
Technical Textile raises global profile
Textile innovations by the Technical Textiles Research Centre were presented the leading worldwide conference for nonwovens, EDANA
Uni experts at major wound care conference
The 6th International Skin and Infection Prevention Conference was titled Innovations in Wound Management: Welcome to Tomorrow’s Reality
Cancer sufferers’ hair loss misery could be over
Researchers are developing a lotion which, combined with scalp cooling innovations, could put an end to the misery for many cancer sufferers